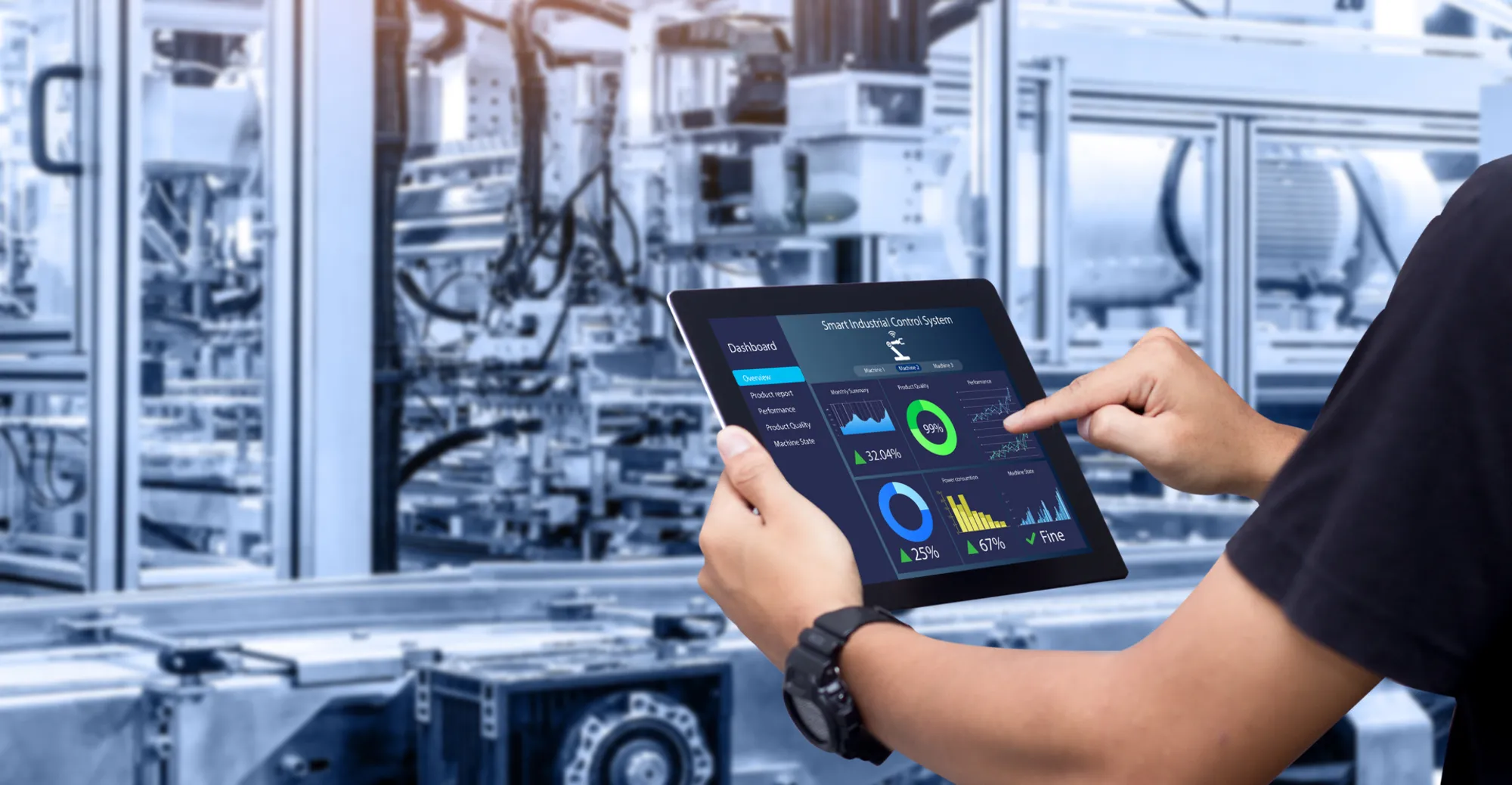
Sustainability: smart design of HVAC spaces
Sustainability: smart design of HVAC spaces
– by Jeroen Fijan, 18/05/21
The energy efficiency of two HVAC designs can be widely different even when their conditions and air amounts are the same. How is this possible? By smart design of the AC zones and the tactical placement of technical spaces with the air-handlers and vertical duct shafts in the centre of a zone.
There is a correlation between amount of air in a HVAC system and the volume of the AC room where the air handling unit is placed. Dividing the ship into different AC zones as efficiently as possible creates the perfect air volume/technical space volume ratio. But that’s not all: placing the AC room in the right position leads to a multitude of benefits that greatly improve the overall sustainability of the HVAC system.
Save on weight
More air means more and bigger ducts, which translates into a higher weight. The amount of air needed to meet the specified conditions is determined by transmission calculations and cannot therefore be changed. Using smart design, on the other hand, allows for significant reductions in the amount of ducting.
Let’s say that the overall amount of air for an area is 10,000 m³/h. In one situation the technical space is placed on the boundary of the AC zone. All the ducts come from the same side, resulting in bigger duct dimensions and bulkhead penetrations. In the other situation, the technical space is positioned more tactically in the centre of the AC zone.
example of smart design
This is an oversimplified example in order to give you an idea. In practice there are more factors to consider, such as the ship’s structure and fire and watertight zones.
Reduced energy consumption
Bringing air from one part of the ship (AC room) to a cabin thirty metres further costs energy, especially when it is meandering through a complex duct system. The resistance of a duct system with all its bends and flaps is overcome by the head pressure of the fan. A higher head pressure obviously results in more power consumption.
As well as saving on weight, cutting the duct system in half by smart design reduces energy consumption as the smaller fans used do not need such a high head pressure. We should also consider that the resistance depends on the air speed and will increase quadratically at higher speeds.
Reduction of valves
An HVAC system contains a range of different valves such as watertight valves, fire dampers, closing valves and smoke dampers. Each valve has a weight, creates air resistance and uses electricity, with most also needing a penetration. It is best then to keep the number of valves in the system to a minimum.
Smart design of AC zones contributes to a reduction in unnecessary valves. This requires a clear overview of the fire zones in a ship and the positioning of watertight bulkheads. Not that they shouldn’t be trespassed, sometimes this is unavoidable, but dividing the AC zone so that it fits inside a fire zone or watertight area can save a lot of valves.
Conclusion
Much of this might seem quite obvious and indeed it is but the reality can be quite a puzzle. Our advice is to start thinking about AC zones as early as possible in the pre-engineering phase.
Another benefit of the smart division of AC zones is the option to save energy when a zone is not in use. For example, you can build energy-saving options into the software for when certain zones like crew, guest or owner areas are unoccupied. Re-heaters can be switched off or set to operate when relative humidity exceeds a certain set point, and you can have central temperature control on recirculation air.
From a financial point of view, the advantages are obvious. Fewer ducts and valves and a shorter installation time saves you both energy and money.
Like to know more about energy-efficient HVAC solutions in the maritime sector? Keep an eye on our site.
Jeroen Fijan | R&D Manager
Jeroen Fijan has been working at Heinen & Hopman since 2001. He started as a draughtsman and, over the years, worked his way up to the top of the R&D division. Sustainability is a top priority in the quest to improve H&H’s products and processes.