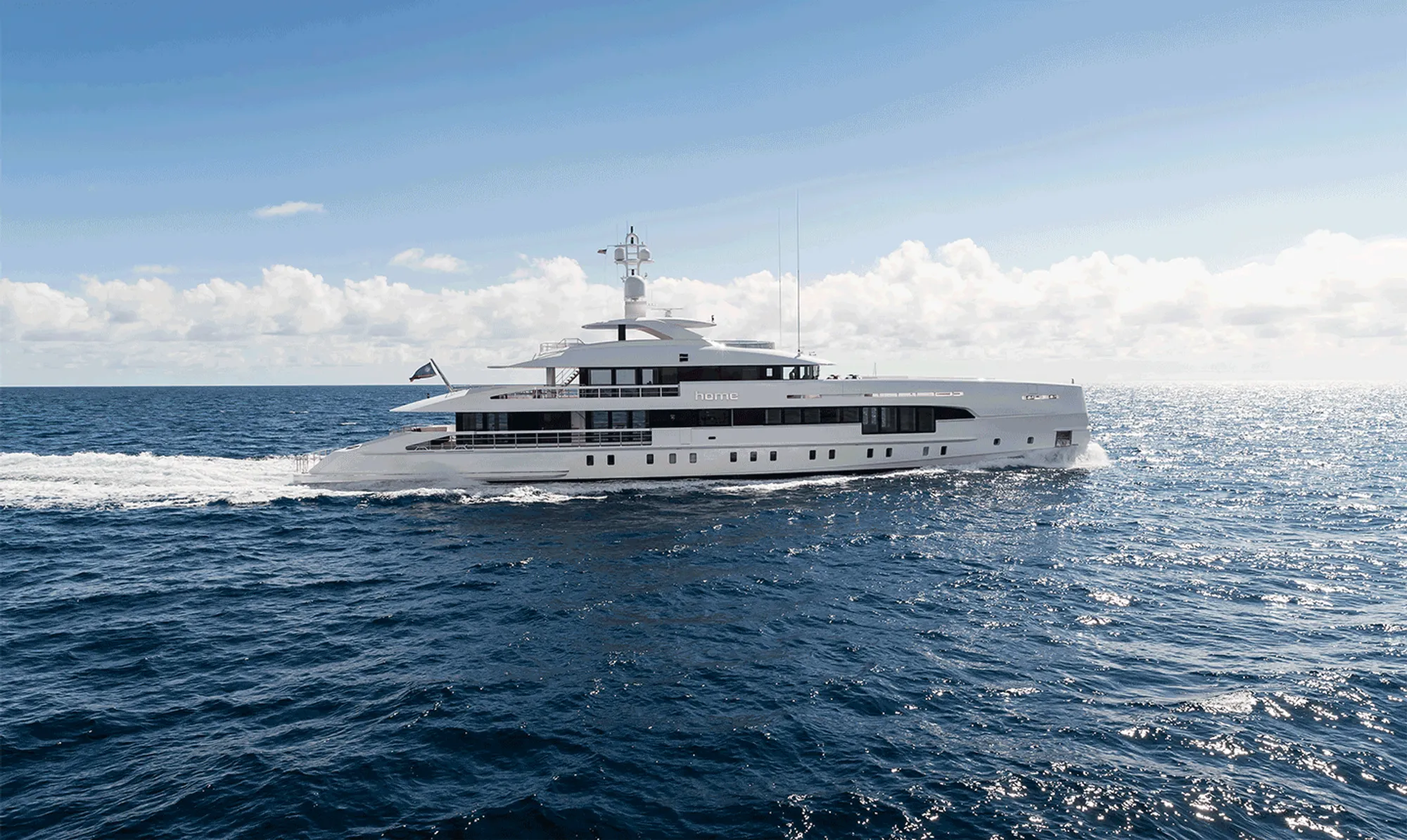
Compressor oil: more than just a lubricant
Compressor oil: more than just a lubricant.
– by Sebastiaan Jansen, 21/01/2020
What is the function of oil inside a compressor? Sebastiaan Jansen sheds light on this topic, explaining what to look out for when selecting oil and how oil tells you something about the condition of your cooling system.
The function of oil
Oil in a compressor system has different functions but is primarily there to prevent friction. A compressor is a mechanical machine with parts like pistons or scrolls, or other parts that are constantly interacting with each other. Friction leads to:
- Energy loss;
- Overheating;
- Noise.
From an energy point of view, it is important that the compressor runs as smoothly as possible. Lubricating oil reduces friction, ensures heat dissipation and seals the compressor, transforming most of the energy put into the compressor into work.
How oil management works
Compressors are part of a cooling cycle, which mainly consists of a condenser, expansion valve and evaporator. Oil only contributes to the compressor (and some valves) – which are the only mechanical parts in the installation. In fact, if oil reaches the condenser and evaporator it will reduce the efficiency of the cooling machine. A mixture of oil and coolant has a lower specific heat.
Many systems have an oil separator built into the pressure line, right after the compressor. This ensures that most of the oil is returned to the compressor and stopped from reaching other parts of the cooling cycle.
Nonetheless, not all the oil is separated and there will always be a small part mixed into the refrigerant.
Points of attention
Not every oil is suitable and it’s important to select the right oil/refrigerant combination. Various oils are available, each with their own viscosity. The higher the viscosity, the thicker the oil. Compressor manufacturers mainly specify the suitable oil types based on viscosity.
From a preventive point of view, we advise changing your oil every five years. Ultimately, however, it depends on how well the chilled water system is running.
In fact, oil is a good indicator of your system’s health.
For example, if the oil contains iron parts it is possible you have a damaged bearing. Should the oil contain copper then there is probably some kind of acidification happening in your system. Is the oil discoloured? Then the system is becoming too hot. The colour of the oil can tell you much about the system.
Oil-free compressors
In 2001, Danfoss launched the Turbocor compressor which has its shaft captured in a magnetic field. The resulting lack of mechanical friction means oil is not needed and the compressor is lighter and quieter. Absence of oil means no disposal of oil, contributing to a cleaner environment.
The Turbocor compressor is a high-tech machine full of electric circuits. This makes it more vulnerable to errors than a conventional compressor and you need to be highly skilled to perform proper maintenance.
In conclusion, while the Danfoss oil-free compressor is a beautiful machine, it is not always the best solution. Every system is different, just as every vessel is a unique product in her own right. Choosing the most suitable compressor is a balancing act between performance, efficiency and costs.
Should you have any questions about selecting the right compressor oil or carrying out maintenance, simply contact one of our technicians. We will be pleased to help you achieve the best possible solution.
Sebastiaan Jansen | Manager Cooling Department
Sebastiaan Jansen has been working at Heinen & Hopman since 1997. He started as assistant mechanic at our company and worked his way up to the position of Manager Cooling Department. Sebastiaan and his team are responsible for the engineering of the cooling systems for all kinds of Heinen & Hopman projects. He aims to achieve the highest quality systems through applying innovative technologies. A challenging, but interesting, task.